Building the Skeletal Framework for the Streetlamp that will Act as a Conduit for Wiring and Support the LEDs AND Trolley Overhead! Crazy Project I Know...
Built of brass, this armature performs three functions. 1. Support the LEDs so that the streetlamp will light up. 2. The brass tube is a conduit for the positive wires and the brass itself is the ground. 3. The loop at the top of this assembly is a tie off for the trolley span wires. Then this armature will be placed in a rubber mold and resin will be poured around it creating an ornate streetlamp! That's the plan anyway. Yes sir- that's the plan!
The basis for the armature is a 3/32" brass tube. A brass rod that has been drilled to accept a brass wire loop soldered on, is inserted into the tube just above where the holes for the wires are drilled.
The negative lead of the LED is bent and soldered to the brass. The positive lead is trimmed short and a thin wire is soldered on and then threaded down the tube which will protrude under the layout where the resister and electrical hookups reside.
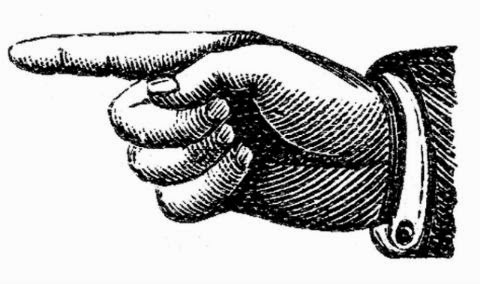
The resin will cover the bulbs so I milled lamp globes out of acrylic tube to fill in the space in the rubber mold.
The acrylic tube fits over the LED perfectly. An Acrylic rod is inserted in the top of the tube to fill in above the LED where the fancy curves of the lamp globe will be carved in.
Then spinning the acrylic a small file shaves it into shape.
Before and after.
Wholly Katz! Its lit! It works! This thing is actually working so far! This project might actually pan out after all.
Alright! Well! This is how the armature fits in the mold. Next week I'll pour the resin and we'll see if we get a respectable looking streetlamp. Yes sir! We'll see if we get a respectable looking streetlamp out of all this!
Dandy